Implementasi 5 Whys di Warehouse untuk Peningkatan Efisiensi
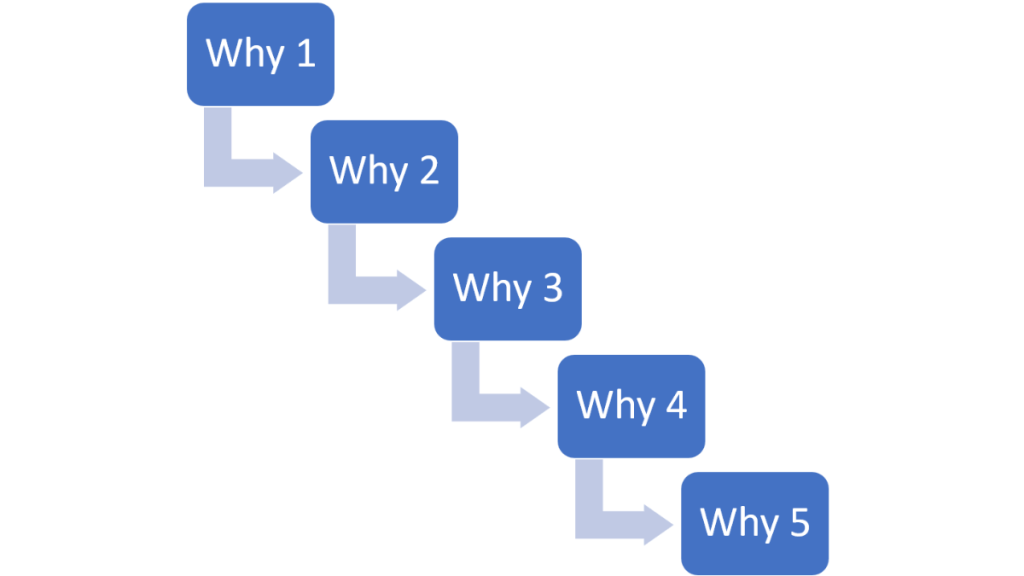
Efisiensi operasional menjadi aspek kunci dalam manajemen gudang yang sukses. Setiap gangguan atau masalah yang muncul di gudang, mulai dari keterlambatan pengiriman hingga kesalahan stok, dapat berdampak besar pada kinerja perusahaan secara keseluruhan. Salah satu metode efektif yang dapat digunakan untuk mengidentifikasi dan mengatasi akar penyebab masalah adalah metode 5 Why. Metode ini memungkinkan manajer gudang untuk menggali lebih dalam tentang akar penyebab masalah melalui pertanyaan yang sederhana namun mendalam, yaitu “Mengapa?” hingga lima kali.
Pada panduan ini, kita akan membahas secara rinci tentang implementasi metode 5 Why di lingkungan gudang dan bagaimana penerapannya dapat meningkatkan efisiensi operasional secara signifikan.
Apa Itu Metode 5 Why?
Metode 5 Why adalah teknik analisis yang digunakan untuk mengidentifikasi akar penyebab dari suatu masalah dengan cara bertanya “mengapa” secara berturut-turut hingga ditemukan penyebab mendasar. Teknik ini diperkenalkan oleh Sakichi Toyoda, pendiri Toyota, dan telah menjadi bagian integral dari sistem manajemen lean yang bertujuan untuk meningkatkan efisiensi dan mengurangi pemborosan dalam proses produksi dan logistik.
Dalam konteks gudang, metode ini sangat efektif digunakan untuk menganalisis masalah yang kompleks sekalipun. Dengan mengajukan pertanyaan yang tepat dan mendalam, akar masalah dapat ditemukan, dan solusi yang lebih tepat sasaran dapat diterapkan.
Pentingnya Implementasi Metode 5 Why di Warehouse
Lingkungan gudang sering kali menghadapi berbagai masalah yang memengaruhi efisiensi operasional, seperti kesalahan dalam manajemen stok, keterlambatan pengiriman, atau kerusakan barang. Banyak dari masalah tersebut sering kali hanya diatasi di permukaan tanpa menyelesaikan akar penyebabnya, sehingga masalah yang sama terus berulang. Implementasi metode 5 Why dapat membantu mengubah pendekatan ini.
Dengan metode 5 Why, setiap masalah dianalisis secara mendalam untuk menemukan penyebab utama, bukan hanya gejala masalah. Hal ini memungkinkan manajer gudang untuk merancang solusi yang lebih efektif dan mencegah masalah serupa terjadi di masa depan.
Manfaat Utama Menggunakan 5 Why di Gudang:
- Identifikasi akar penyebab masalah secara efektif.
- Pengambilan keputusan yang lebih tepat dengan pemahaman mendalam tentang masalah.
- Peningkatan efisiensi operasional melalui solusi yang lebih terfokus dan tepat sasaran.
- Pengurangan risiko terulangnya masalah karena akar penyebabnya telah diidentifikasi dan diatasi.
Langkah-langkah Implementasi Metode 5 Why di Warehouse
1. Identifikasi Masalah
Langkah pertama yang harus dilakukan adalah mengidentifikasi masalah yang terjadi di gudang. Masalah ini bisa bermacam-macam, mulai dari keterlambatan pengiriman, kesalahan dalam penghitungan stok, hingga kerusakan barang selama proses penyimpanan. Pada tahap ini, penting untuk mendefinisikan masalah dengan jelas sehingga analisis selanjutnya dapat berjalan dengan lebih terarah.
Contoh masalah: Pengiriman barang terlambat ke pelanggan.
2. Bentuk Tim yang Tepat
Selanjutnya, bentuk tim yang terdiri dari individu-individu yang memahami proses dan masalah yang terjadi di gudang. Tim ini harus mencakup anggota dari berbagai departemen yang relevan dengan masalah yang dihadapi, seperti tim operasional, tim administrasi gudang, dan tim pengiriman.
Keberagaman dalam tim ini penting karena berbagai perspektif diperlukan untuk mendapatkan gambaran yang komprehensif tentang masalah yang dihadapi.
3. Ajukan Pertanyaan “Why” Hingga Lima Kali
Pada tahap ini, untuk setiap masalah yang diidentifikasi, ajukan pertanyaan “Why” secara berurutan hingga lima kali untuk menemukan akar penyebab dari masalah tersebut. Metode ini membantu menguraikan masalah dari gejala ke penyebab mendasar yang sering kali tidak terlihat pada analisis pertama.
Contoh: Masalah: Pengiriman barang terlambat.
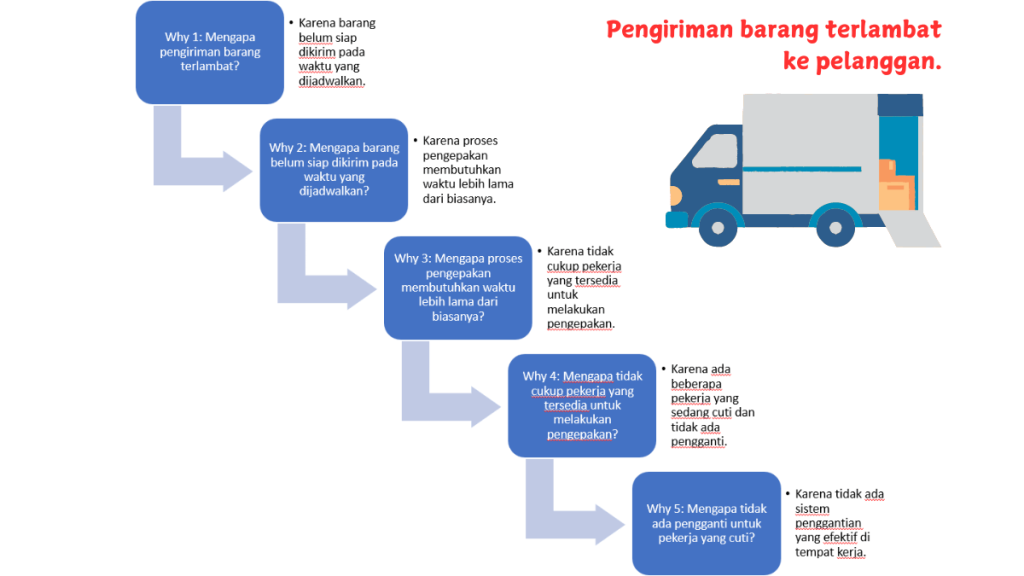
Dari contoh ini, kita dapat melihat bahwa akar penyebab masalah pengiriman terlambat adalah tidak adanya sistem penggantian yang efektif untuk pekerja yang cuti. Jika hanya memperbaiki gejala masalah (misalnya, mempercepat pengiriman barang), masalah yang sama kemungkinan besar akan muncul kembali.
4. Identifikasi Akar Penyebab
Setelah pertanyaan “Why” diajukan hingga lima kali, tim akan dapat mengidentifikasi akar penyebab dari masalah tersebut. Dalam contoh sebelumnya, akar penyebab dari keterlambatan pengiriman adalah tidak adanya sistem penggantian yang efektif.
Tahap ini sangat penting karena solusi yang efektif hanya dapat dirancang jika akar penyebab masalah telah diidentifikasi dengan jelas.
5. Tentukan Solusi yang Tepat
Setelah akar penyebab masalah ditemukan, langkah berikutnya adalah menentukan solusi yang tepat untuk mengatasi masalah tersebut. Solusi ini harus fokus pada penghilangan akar penyebab masalah, bukan hanya memperbaiki gejalanya.
Contoh solusi:
Dalam kasus keterlambatan pengiriman yang disebabkan oleh kurangnya pekerja karena tidak ada sistem penggantian, solusinya mungkin melibatkan pengembangan dan implementasi sistem penggantian pekerja yang lebih efektif, seperti menyediakan pekerja cadangan atau mengatur jadwal cuti dengan lebih baik.
6. Implementasi dan Evaluasi
Setelah solusi ditentukan, langkah selanjutnya adalah mengimplementasikan solusi tersebut di gudang. Pastikan bahwa semua anggota tim dan pekerja gudang memahami langkah-langkah yang harus diambil untuk menerapkan solusi.
Setelah implementasi, penting untuk melakukan evaluasi untuk menilai apakah solusi yang diterapkan berhasil mengatasi masalah. Evaluasi ini juga mencakup pemantauan jangka panjang untuk memastikan bahwa masalah yang sama tidak muncul kembali.
7. Dokumentasi
Terakhir, pastikan bahwa seluruh proses, dari identifikasi masalah hingga penerapan solusi, didokumentasikan dengan baik. Dokumentasi ini penting sebagai referensi di masa depan jika masalah serupa terjadi lagi, sehingga tim dapat merujuk pada solusi yang sudah pernah diterapkan sebelumnya.
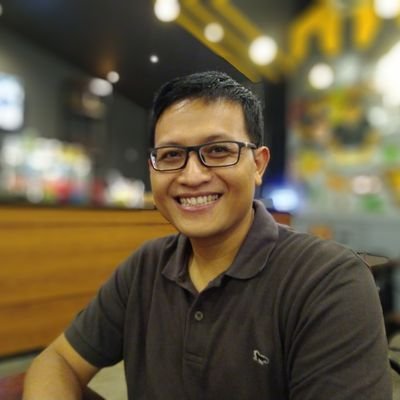
Logistics Enthusiast
arthanugraha.com.
[email protected]